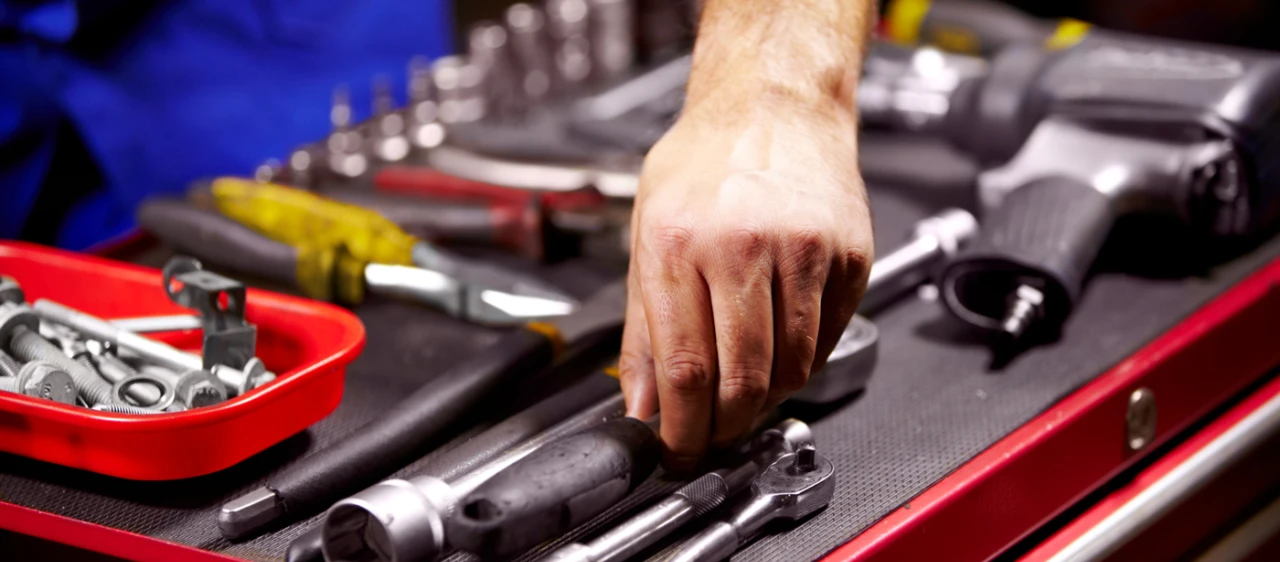
- Products & PPE
- PPE Service Centre
PPE Service Centre
Eurosafe houses a professional and reliable Service Centre where our dedicated team is certified to service a wide range of safety equipment and PPE.
We are a certified Globestock, MSA, and Ridgegear channel partner, and this enables us to service and carry out repairs to their branded products.
If you own work equipment that is used to protect your employees from a fall from height, you have a legal duty to ensure that it is inspected at suitable intervals (Regulation 12 (3) of the Work at Height Regulations 2005). The inspection must be undertaken by a competent person, who has the relevant knowledge, training, and experience in the subject.
Eurosafe specialists are available to provide expert advice to our customers, so they fully understand what the servicing entails and why this helps them get the best out of their safety equipment.
We carry out a thorough visual inspection of all components, checking the red deployment indicator, the cable for kinks, birdcaging, frays, and other damage, and all external parts for damage or excess corrosion.
A full function test is carried out checking for device lock, recoil, and operation of retraction system along with listening for tell-tale clicking as the cable retracts.
Frequent repairs can include the replacement of cables and energy absorbers due to a deployment. This involves the removal of components, slight re-tensioning of the spring on replacement of the energy absorber and a new cover gasket along with deep cleaning of revealed areas of the device. Occasionally, attachment points of a certain type fail due to excessive corrosion and as these are a key component of the device, these are replaced along with new bolts and a lockable tab washer.
At Eurosafe, we endeavour to repair all devices rather than replace them due to seemingly unrepairable problems. The most common are sheared studs which we can remove and replace in 95% of cases. This saves expensive device replacement costs and keeps the existing units in service for as long as they operate at their optimum level.
We carry out a thorough visual inspection of all components, checking the red deployment indicator, the cable for kinks, birdcaging, frays, and other damage, and the casing for cracks and other damage.
A full function test is carried out checking for device lock, recoil, and operation of the retraction system along with listening for tell-tale clicking as the cable retracts.
The service includes the above along with the removal of the casing and checking the torque values on internal bolts. Any found to be insufficiently torqued are removed, thread lock is applied, and the bolts are re-torqued to the specified level. While the casing is removed, we can inspect the internals, check all the toothed mechanisms for wear, ensure all locking pawls are in good condition and all other components are working safely and efficiently. A deep clean and lubrication of all relevant components are carried out to ensure optimum performance.
Repairs are very similar to sealed SRL’s but due to their locations, the standard SRL’s don’t receive the harsh treatment due to the differences in where they are used, and the environments they operate in.
These devices undergo a thorough checklist covering measurement and performance, including tolerance checks for wear areas. Visual inspections cover damage, corrosion, and the integrity of swivels, rivets, and fastenings.
Drop tests and function checks are conducted and recorded. Webbing connectors and shock packs are date-checked, while karabiners undergo checks for functionality, corrosion, and wear.
Common repairs include replacing the cover and yellow buffer for the anti-inversion pin housing, along with lubricating and installing a new pin for safe operation. Webbing connectors are replaced due to obsolescence, and damaged or missing ID labels are also addressed.
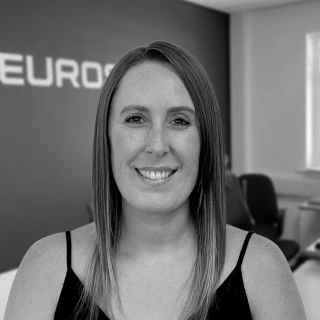