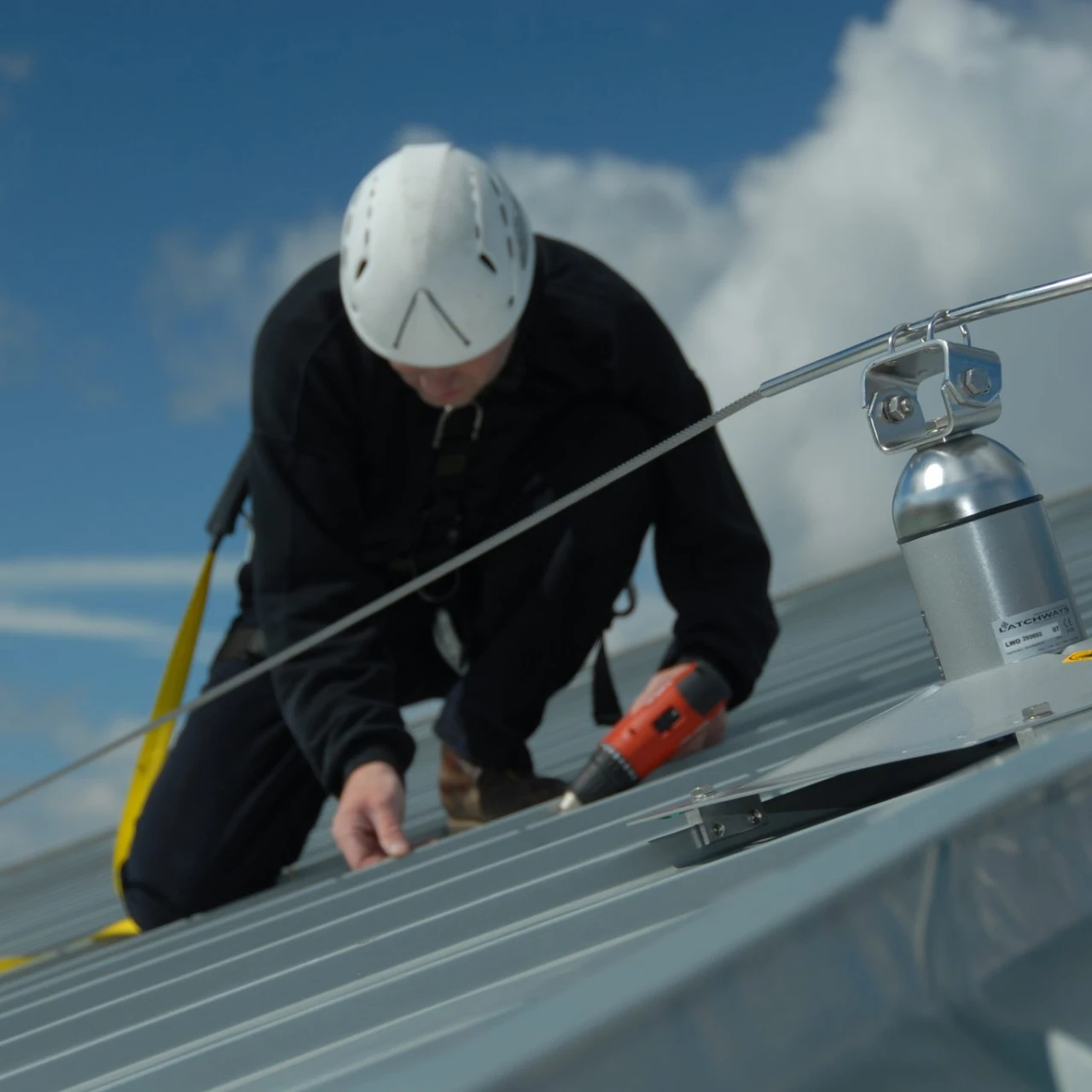
- Knowledge Base
- Tips & Explanations
- Everything you need to know about BS 7883:2019
Everything you need to know about BS 7883:2019
In the past five years, falls from heights have constituted 26% of all fatal accident injuries, resulting in an average of 37 fatalities per year.
To mitigate such risks, personal fall protection equipment (PFPE) has been specifically designed to provide adequate protection for individuals working at elevated positions. Among the crucial elements of PFPE, anchor systems play a critical role.
We have prepared this overview to assist you in achieving compliance with the latest height safety standard BS 7883:2019. By following the best practices outlined in this guide, you will gain a thorough understanding of how to ensure the utmost safety for those working at heights.
The 2019 revision considers the advances within fall protection technology and includes guidance across 5 types of common anchor systems:
Type A – Permanently fixed anchor system that incorporates one or more structural anchors such as an eyebolt.
Type B – A removable and transportable anchor that does not incorporate a structural anchor so is not fixed to a structure.
Type C – A structurally anchored anchorage system featuring a flexible anchor line such as a wire rope, fibred rope, or webbing.
Type D – A structurally anchored anchorage system incorporating a tube or rigid rail anchor line.
Type E – Anchor device which relies solely on mass and friction between itself and the load-bearing surface. It also introduces the role of the system designer who has overall responsibility for producing a system technical file, an operations & maintenance manual, and an examination scheme.
These documents should be passed to the duty holder for the life of the system(s) and made available to anyone using, and/or undertaking future inspections and maintenance of the anchorage system(s).
Where elements of the anchor system are hidden reverse engineering design checks will involve opening/lifting of the roof substrate to gain full access to the anchor device, structural anchors, and base material to confirm through design calculations and information supplied by the manufacturer, overall suitability of the anchor system. The information and evidence gathered will be required to form part of the technical file.
System Technical File: In summary, this should include records of the system design/layout, design calculations, structural fixing details, as-built drawings, and information on any hidden elements.
Operations and Maintenance Manual: In summary, this should include user instructions, personal fall protection equipment (PFPE) required, method statement for use, and rescue and recovery plan.
Examination Scheme for Inspections: Recommendations for inspection supplied by the manufacturer(s) / suppliers of the personal fall protection system (PFPS) and frequency of periodic inspections.
If any of the above documents are not available, then an installation review would be required to be undertaken. If information on hidden elements is not available, this may require reverse engineering.
Where elements of the anchor system are hidden reverse engineering design checks will involve opening/lifting of the roof substrate to gain full access to the anchor device, structural anchors, and base material to confirm through design calculations and information supplied by the manufacturer, overall suitability of the anchor system. The information and evidence gathered will be required to form part of the technical file.
Following the standard, if the information required under BS 7883:2019 is not available prior to the inspection or cannot be gathered on the day then yes, the system(s) could conditionally fail. However, if some information is available and a physical test can be completed successfully, (where the fixing background is known/unquestionable) then they could conditionally pass with an advisory note to have the required documentation produced for the missing elements within an appropriate completion timescale.
Any required actions should be completed as soon as reasonably practicable or within an appropriate completion timescale. Should the actions not be implemented within the appropriate timescale, then they could conditionally fail on the next inspection.
Eurosafe can work with you to produce a System Technical File, Operations & Maintenance Manual, and Examination Scheme for Inspection. Prices would reflect the level of difficulty accordingly.
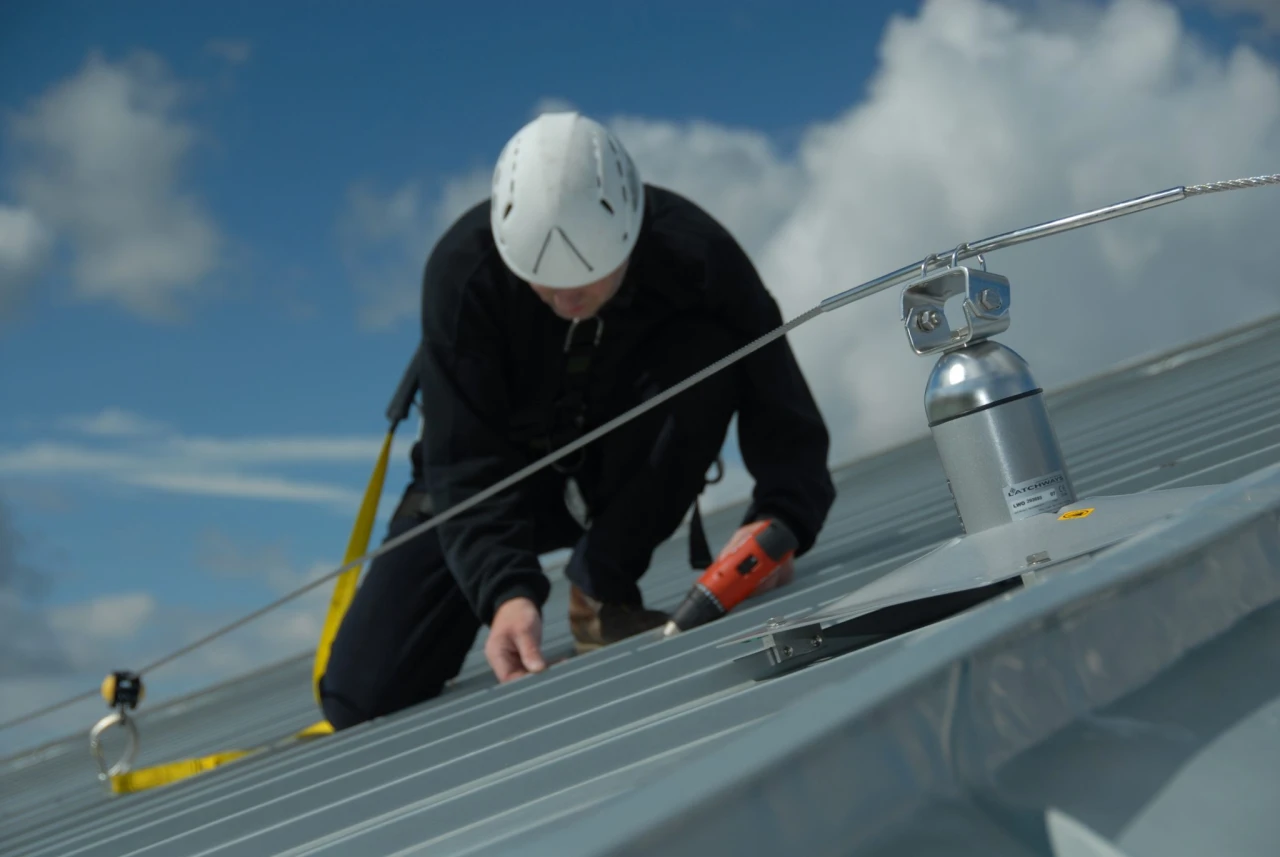
Inspection Outcomes Explained
Previous versions of the standard allowed for some ambiguity in interpreting the criteria for determining pass or fail results. However, the most recent iteration of the British Standard has effectively resolved this issue by introducing four distinct category results:
PASS: Satisfies all relevant recommendations. This allows the equipment to remain in use and be labelled as remaining in service.
CONDITIONAL PASS: The anchorage system satisfies the recommendations of BS 7883:2019, a previous standard or code of practice, and does not present any immediate safety concern so it should be labelled as remaining in service. However, an inspection report should be presented to the duty holder with recommendations on remedial work required to improve the anchor device within an appropriate completion timescale.
CONDITIONAL FAIL: This represents an immediate safety concern and requires the anchor system and/or PFPE to be taken out of service and labelled accordingly or decommissioned to prevent use. In these cases, the safety concern can be rectified so the duty holder should be presented with a detailed inspection report including remedial works that must be carried out before the anchor system is re-inspected and returned to service.
This result also applies to systems that may have satisfied a previous standard or code of practice but do not conform to all current recommendations.
FAIL: As the result suggests, this represents an immediate safety concern that the anchor system or device cannot be repaired or improved so it should be taken out of service and labelled with “Do Not Use” to avoid any uncertainty. Where possible, the system should be decommissioned to prevent potential use. Permission to physically remove an anchor system or device should be sought from the duty holder.
Together we can help reduce the number of height-related injuries!
The standard has been introduced by the British Standards Institution (BSI) to provide a clear and comprehensive structure to those responsible for the design, installation, maintenance, and inspections. Those who put safety first should follow this standard to ensure they are doing everything in their power to reduce risk which is ultimately why the standard has been introduced.
Eurosafe - Safety Assured, Trust Secured
With a trading history spanning over two decades, Eurosafe Group proudly stands as Europe’s leading specialist in providing fall protection and access solutions. Our team of approximately 300 employees works tirelessly every day to make the world a safer place and is trusted upon thousands of sites nationwide to inspect and certify height safety and access equipment. We understand that safety is a fundamental need for both businesses and individuals. We pride ourselves in building long-term relationships with our customers, based on the solutions we provide.
We understand that this change in the standard may bring challenges to you, our customer. We aim to work with you throughout each stage to ensure you are supported, the staff remains protected and compliance requirements are met.
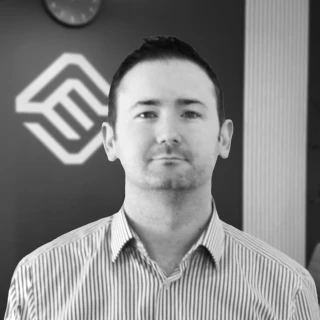