- Inspection & Maintenance FAQs
Inspection & Maintenance FAQs
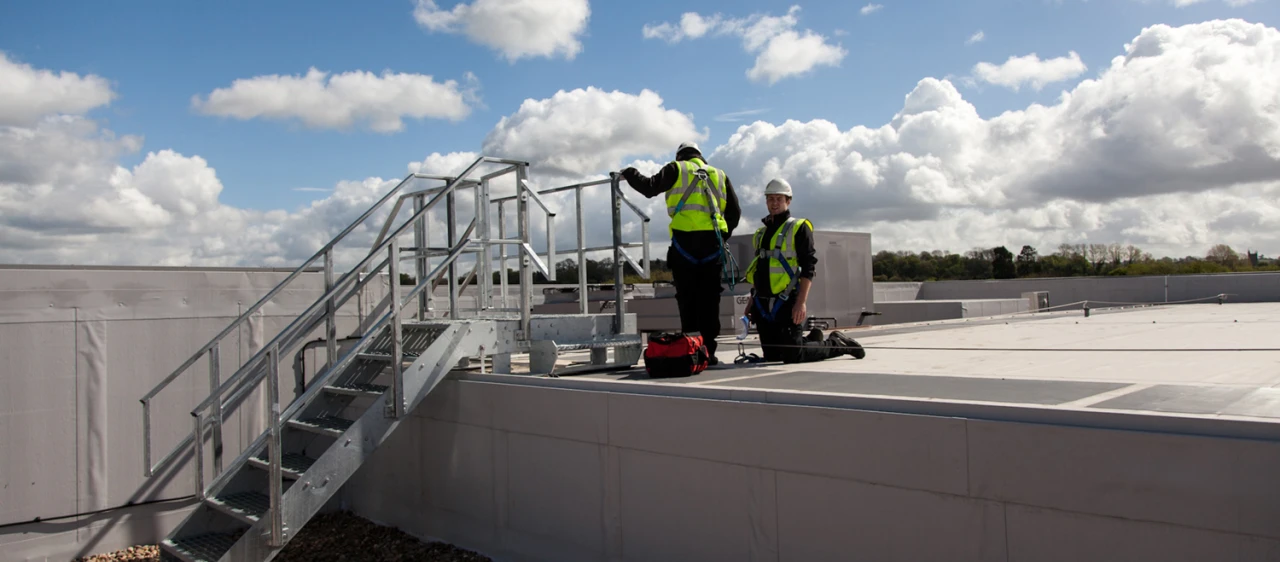
Answer: Yes.
Duty holders have a legal duty to ensure all staff and workers attending their sites are kept safe and free from injury. The Health and Safety at Work etc. Act 1974 (HSWA) requires employers to ensure, so far as is reasonably practicable, the health, safety and welfare at work of all their employees. This includes providing a safe place of work, safe systems of work, and adequate training and supervision. Employers also have a duty to protect others who may be affected by their work activities, such as contractors, visitors, and the public. This is further supported by the Working at Height Regulations 2005 (WAHR) which was introduced to prevent death & injury from falls from height and requires equipment and systems to be inspected and maintained in a safe condition.
The competent party undertaking the inspections will detriment the inspection frequency based on several factors such as risk, usage, and environment. In general, items such as horizontal cable safety systems (often referred to as mansafe) are inspected on a frequency not exceeding 12 monthly intervals. This is also applied to other items such as single-point anchors, ladders, and guardrails. Items that are required to raise and lower personnel such as rope access anchors or abseil rails are generally inspected at frequencies not exceeding 6 monthly intervals as come under the regulation of LOLER.
Yes, Insurance companies carry out a visual inspection/examination to satisfy LOLER 98 and PUWER 98. They would reference reports from the competent testing company for load testing etc and would recommend to clients have the equipment maintained by an approved agent, such as Eurosafe. They would also advise customers to have an approved agent inspect equipment, should they have concerns over the integrity of the system. Insurance companies therefore satisfy Reg. 9 (Thorough Examination) of LOLER where applicable and Reg 6 (Inspection) of PUWER. Eurosafe also covers these elements as part of their inspections along with Reg. 5 (Maintenance). This approach is seen as best practice as LOLER speaks about the competent person being sufficiently independent and impartial.
Yes, Duty holders have a legal duty to ensure all staff and workers attending their sites are kept safe and free from injury. The Health and Safety at Work etc. Act 1974 (HSWA) requires employers to ensure, so far as is reasonably practicable, the health, safety, and welfare at work of all their employees. The Electricity at Work Regulations 1989 state that all electrical installations, including lightning protection systems, must be maintained in a safe condition. Where lightning protection is installed, this needs to be maintained at frequencies not exceeding 12 months to ensure it is safe, fit for purpose and limit the risk to the duty holder.
Yes, there has been lots of improvements but one of the main changes is how inspection outcomes are recorded. Previous versions of the standard left the pass or fail result criteria open to some interpretation. The latest version of the Standard has addressed this and introduced 4 clear and concise category results along with detailing the information required to be gathered as part of an installation review.